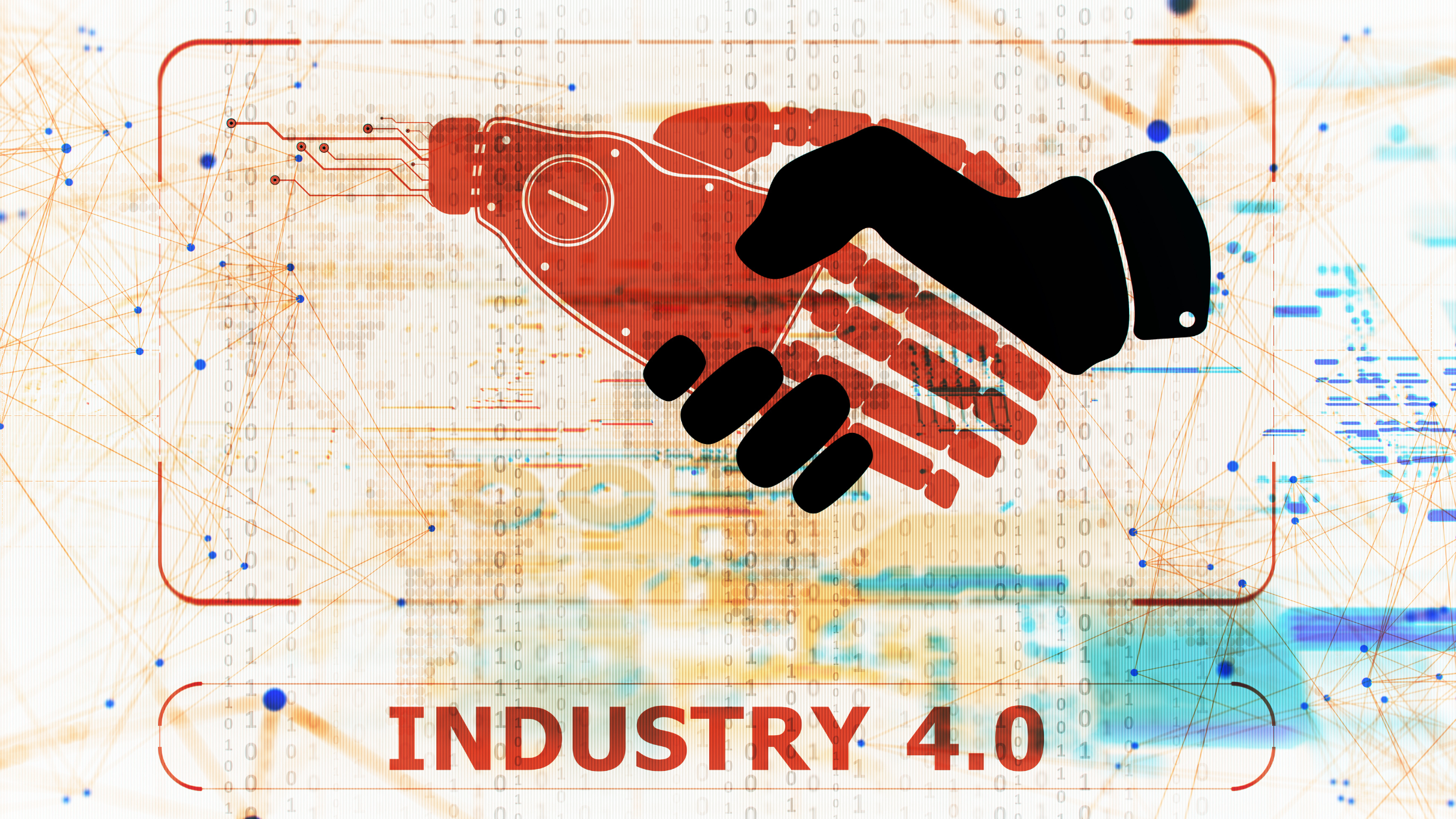
Industry 4.0 Technologies: Reshaping the Landscape of the Future Manufacturing Workforce
Picture this: You're a manufacturing executive, and the future of your industry seems as unpredictable as a game of high-stakes poker. The cards? A dizzying array of Industry 4.0 technologies. The stakes? The very survival of your business and the livelihoods of your workforce.
As we stand in 2025, the manufacturing landscape is evolving at breaking steed. The Industrial Internet of Things (IIoT) market is projected to reach $87.9 billion by 2026, growing at a CAGR of 11.9%. Smart factories, once the stuff of science fiction, are now becoming a reality, with the innovative manufacturing technology sector forecasted to hit $787.54 billion by 2030.
But here's the crux: while these technologies promise unprecedented efficiency and productivity, they're also reshaping the workforce profoundly. Integrating Industry 4.0 technologies redistributes work between machines and people, shifting tasks from manual operations to remote management and data processing. This transformation is creating cleaner, more creative workplaces but also demands new skills and adaptability from workers.
But don't despair! There's hope on the horizon. The solution lies in understanding these technologies and their impact on the workforce. By understanding how these technologies are progressing and the changes in talent management, companies can strategically plan and implement strategies that address these changing factors.
This blog will explore the core technologies driving Industry 4.0 and their future outlooks, from cloud computing to digital twins and additive manufacturing. We'll examine their future outlook and how they're reshaping the workforce. Whether you are a seasoned manufacturing professional or a worker looking to future-proof your career, this blog will equip you with the knowledge to thrive in the new industrial landscape.
Industry 4.0: A New Era of Manufacturing
The onset of Industry 4.0 marks a revolutionary shift in manufacturing and industrial processes, marking an era where digital technologies seamlessly intertwine with traditional practices. This innovative approach aims to create more efficient and predictive manufacturing environments, seen through the emergence of "Smart Factories".
These advanced factories harness cutting-edge technologies to boost productivity, streamline operations, and enhance adaptability across manufacturing and supply chain processes. At the heart of this technological evolution lies the convergence of several key elements:
Information Technology (IT) Integration: This encompasses the unification of infrastructure applications, data management systems, and robust security protocols.
Enterprise Resource Optimisation: The merging of various business process tools and strategies, spanning from sophisticated supply chain management (SCM) to advanced customer relationship management (CRM) systems.
Operational Technology (OT) Convergence: This involves the integration of technologies across the entire production spectrum, from factory floors and warehouses to final delivery mechanisms.
The driving force behind Industry 4.0 is the integration of these business processes, IT systems, and operational technologies. Data serves as the crucial link binding these elements together.
By analysing information from diverse sources - including structured and unstructured business data, IT system logs, and operational metrics - companies can uncover intelligent correlations. These insights enable predictive analysis, empowering businesses to make proactive, data-driven decisions that shape the future of manufacturing.
The Evolution of the Industrial Revolution
To fully appreciate the significance of Industry 4.0, it's essential to understand its place in the broader context of industrial revolutions:
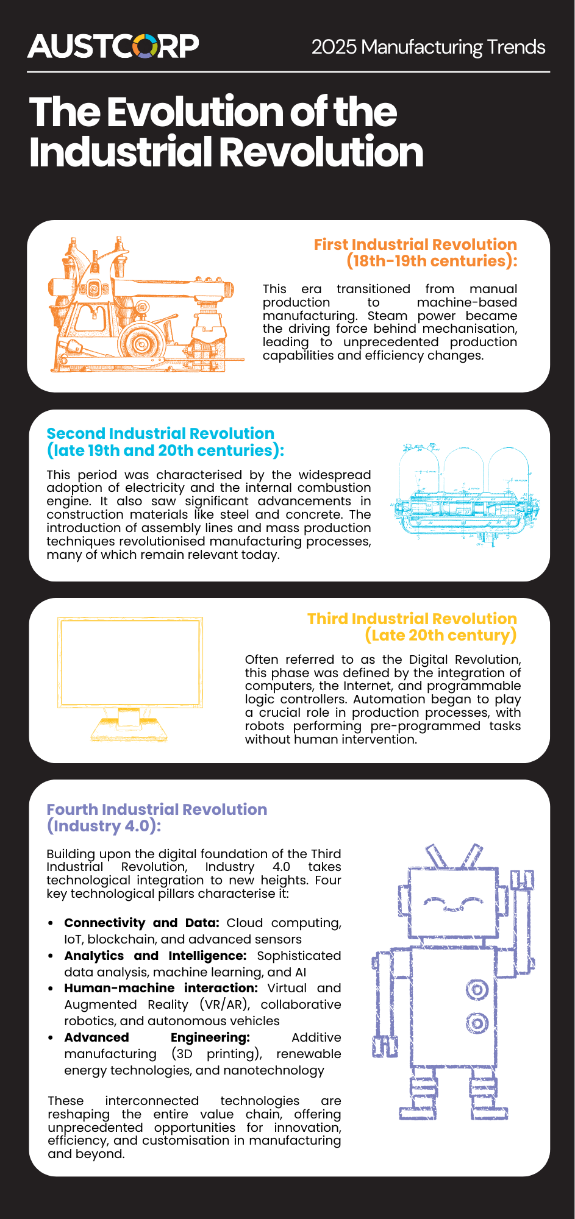
Technologies driving Industry 4.0 and their Future Outlook
Cloud Computing:
Cloud technology is the backbone of Industry 4.0, supporting the implementation of advanced technologies like artificial intelligence, machine learning, and Internet of Things (IoT) integration. It enables seamless communication and coordination between cyber-physical systems, facilitating efficient data exchange and enhancing the ability to design, monitor, and manage innovative, flexible, automated, and self-optimising production processes.
As we look towards 2025, three significant trends in cloud computing are emerging:
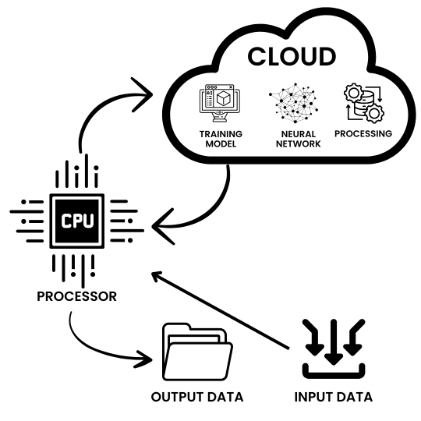
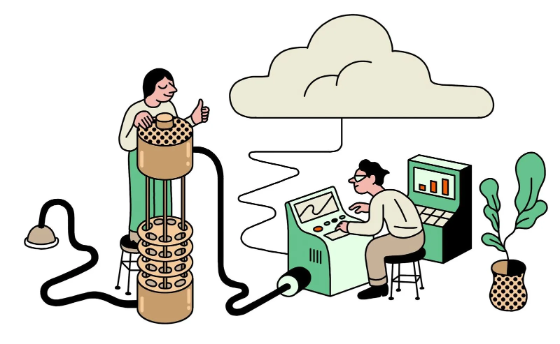
AI and Machine Learning Integration in Cloud Environments: Traditional cloud platforms increasingly incorporate AI and Machine Learning (ML) capabilities to leverage next-generation computational power. These advanced algorithms can process vast amounts of cloud-stored data to identify opportunities for optimisation, cost reduction, and proactive preventive measures. The continuous learning nature of ML algorithms means that efficiency improvements are ongoing as new data is processed and analysed.
The Promise of Quantum Cloud Computing: While still in its infancy, quantum cloud computing holds immense potential for achieving unprecedented processing speeds in complex operational scenarios with multiple variables. This cutting-edge technology could transform manufacturing processes by enabling multi-scale simulations of material properties. For instance, in pharmaceutical manufacturing, quantum computing could allow for precise modelling of molecular structures, potentially accelerating drug discovery and development timelines.
The Rise of Edge Computing: Edge computing brings data processing closer to the source of data generation, reducing latency and bandwidth requirements. In a manufacturing context, this could be applied to intelligent packaging lines, where sensors detect and sort products based on size and weight in real-time without transmitting large volumes of data to distant servers. This approach is particularly valuable in scenarios requiring instantaneous analysis, such as predictive maintenance or automated quality control in high-speed production environments.
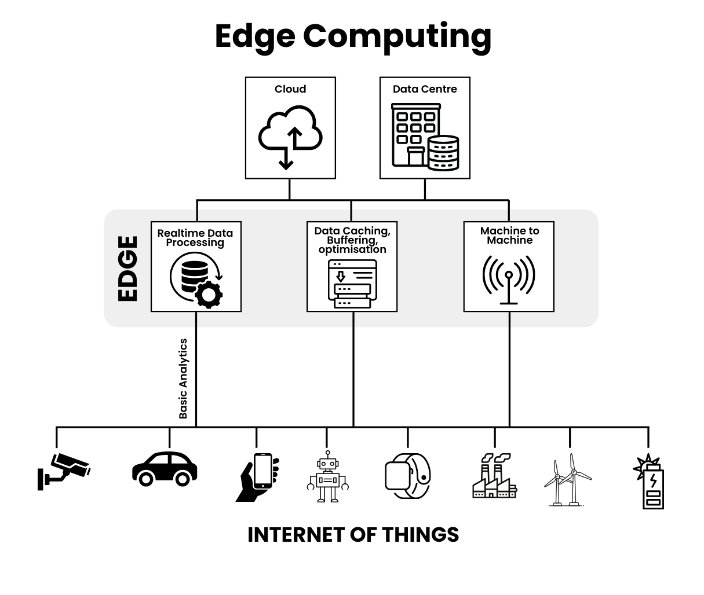
These emerging trends in cloud computing are set to enhance the capabilities of Industry 4.0 technologies further, driving innovation and efficiency in manufacturing processes.
Industrial Internet of Things (IIoT):
The Industrial Internet of Things (IIoT) is emerging as a cornerstone of manufacturing in 2025, with companies increasingly leveraging IoT technologies to transform their production facilities into innovative, adaptive systems capable of process automation and resource optimisation.
The IoT manufacturing market has experienced significant growth, with projections indicating an expansion from $50 billion in 2021 to $87.9 billion by 2026, growing at a CAGR of 11.9%. The accelerating automation of production processes primarily drives this rapid adoption, as IoT enables the creation and optimising of cost-effective, responsive, and efficient system architectures.
Looking ahead, most industrial players are expected to adopt cloud-based IoT platforms. This approach will allow manufacturers to easily scale their data usage, access solutions in real-time, and avoid substantial investments in expensive IT infrastructure. Cloud-based IoT solutions offer flexibility and cost-effectiveness, making them increasingly attractive to manufacturers of all sizes.
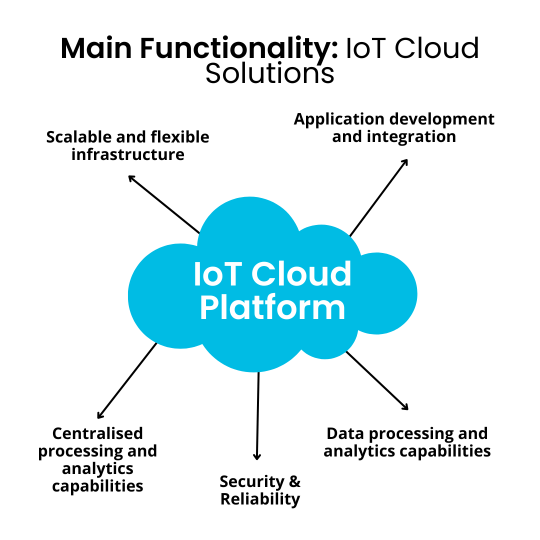
IoT is also set to revolutionise inventory management processes. Many companies will likely integrate IoT technology with advanced tracking systems, enabling manufacturers to monitor inventory throughout the supply chain, from order placement to final delivery. This enhanced visibility will lead to more efficient stock management and reduced waste.
Furthermore, the integration of IoT with other advanced technologies, such as AI, machine learning, and edge computing, is expected to drive even greater efficiencies in manufacturing processes. These combined technologies will enable more sophisticated predictive maintenance, quality control, and production optimisation, further enhancing the value proposition of IIoT in manufacturing.
Smart Factories
Smart factories are at the forefront of a manufacturing revolution, seamlessly integrating machinery, personnel, and extensive data into a cohesive, digitally interconnected system. These advanced facilities harness the power of data analytics to predict trends, suggest optimal operational workflows, and implement automated processes.
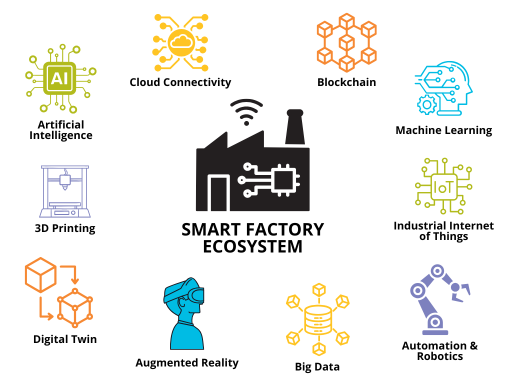
The innovative manufacturing technology sector is on track for remarkable expansion, with forecasts indicating a market value of $787.54 billion by 2030. The research underscores the significant automation potential across industries, with manufacturing, transportation, and warehousing sectors showing up to 60% potential for automation.
The evolution of smart factories is closely tied to other Industry 4.0 technologies:
5G Networks: The rollout of 5G technology, with its minimal latency and high-speed capabilities, is set to transform data processing and collection in smart factories. This advancement will enable more precise, real-time control over production processes, allowing immediate responses to changing conditions. For example, workers equipped with AR/VR headsets will be free to move anywhere on the factory floor and stay connected to the private 5G network.
Edge Computing: This technology is poised to enhance innovative factory operations by processing data closer to its origin on the factory floor. Edge computing reduces delay and speeds up decision-making, which is crucial for maintaining efficiency in fast-paced manufacturing environments.
Collaborative Robots (Cobots): The ongoing development of cobots, supported by Industrial Internet of Things (IIoT) platforms, redefines human-machine interaction in smart factories. These cobots will work alongside human teams, handling repetitive tasks while receiving real-time updates to adjust their actions as needed, becoming an integral part of future intelligent factory setups.
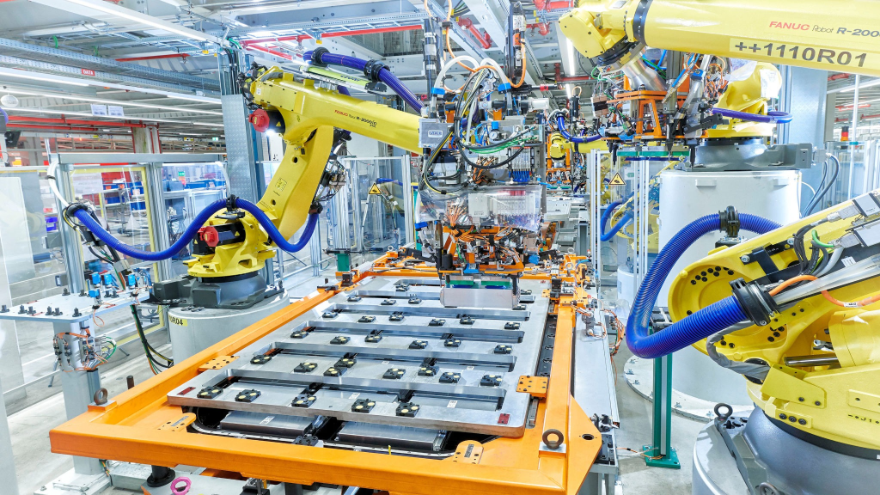
These smart factory technology advancements drive the manufacturing industry towards unprecedented efficiency, productivity, and adaptability.
Digital Twins and Simulation
Digital twins, virtual counterparts of physical assets or processes, are revolutionising manufacturing operations. These real-time digital representations enable efficient, intelligent, cost-effective decision-making in dynamic production environments.
Most industrial executives recognised the technology's relevance to their organisations, with survey data indicating that almost 75% of companies working in advanced industries have already adopted digital-twin technologies that have achieved at least medium levels of complexity.
As we approach 2025, the integration of AI, cloud platforms, and edge computing is poised to drive innovation in digital twin technologies and discrete event simulation. These advancements will facilitate more advanced, real-time, intelligent systems capable of processing vast datasets and making unprecedentedly efficient complex decisions.
The anticipated introduction of 6G networks will provide the infrastructure for handling the extensive data flows required by digital twins and simulations. This next-generation connectivity will enable industries to push the boundaries of real-time simulation and autonomous decision-making through faster data speeds and reduced latency.
Cloud-based discrete event simulation (DES) platforms will continue to be crucial. As companies increasingly move their simulation capabilities to the cloud, they will benefit from scalable, adaptable environments that can handle more extensive, more complex simulations without the limitations of on-site hardware. This shift will enable real-time process optimisation on a broader scale, allowing for the modelling and fine-tuning of entire supply chains.
Moreover, we anticipate closer integration of digital twins with virtual and augmented reality technologies. This combination will create immersive environments for training, engineering, and urban planning, allowing users to interact with digital twins in ways that closely resemble physical manipulation, thereby enhancing design processes and operational insights.
Additive Manufacturing - The Evolution of 3D Printing:
The landscape of 3D printing has dramatically transformed, progressing from single desktop units to sophisticated industrial-scale systems. This progression has been fueled by advancements in materials science, automation, artificial intelligence, and deposition techniques, significantly expanding the capabilities of additive manufacturing.
As we look towards 2025, the future of additive manufacturing is set to be characterised by cloud-connected 3D printers integrated into smart factories. This connectivity will enable direct communication between manufacturing facilities and their customers, allowing on-demand production of customised items. The benefits of this shift include faster turnaround times, innovative supply chain and inventory management approaches, and streamlined product development cycles.
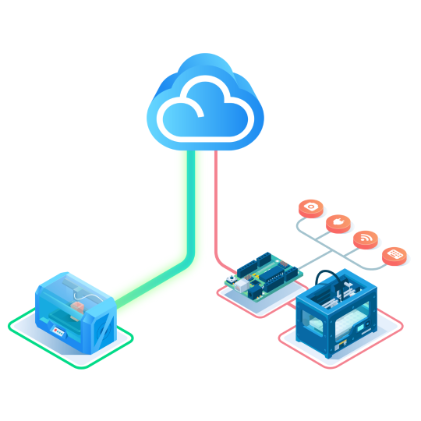
Recent innovations in 3D printing have focused on improving speed and volume while minimising post-processing requirements. A notable advancement is the enhancement of Digital Light Processing (DLP) 3D printing technology, featuring expanded build areas and faster Z-axis printing speeds. These improvements have led to a simplified production process with higher throughput and fewer assembly steps for complex designs. In some cases, these advancements have resulted in 50-90% efficiency gains, marking a significant leap forward in additive manufacturing capabilities.
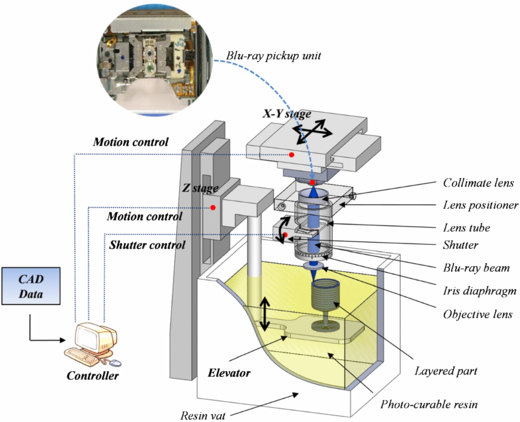
The integration of cloud-based platforms and IoT technologies is further enhancing additive manufacturing's capabilities. Real-time collaboration, file sharing, and remote monitoring are enabling faster design and production processes. Additionally, the rise of large-scale 3D printing is opening new possibilities in industries such as construction, automotive, and energy.
As we approach 2025, the additive manufacturing industry is poised for significant growth, with the market expected to exceed $93.36 billion by 2030, with a compound annual growth rate (CAGR) of 20.3% from 2024 to 2031. This growth is driven by the increasing adoption of 3D printing across various sectors, including aerospace, automotive, and healthcare. The ability to produce complex, customised parts on demand reduces lead times and waste, leading to greater cost efficiency and sustainability in manufacturing processes.
Augmented Reality (AR)
The manufacturing industry is experiencing a significant uptick in augmented reality adoption, mirroring the broader AR market growth. Forecasts indicate that AR manufacturing software could surpass $700 million in value by 2026, accompanied by a rapidly expanding market for industrial-grade AR hardware.
In manufacturing settings, AR systems leverage smart glasses or mobile devices to superimpose digital information onto the physical world. This technology enables workers to access real-time IoT data, digital part representations, repair and assembly instructions, and training materials while interacting with physical equipment or products.
A key area of future development lies in the convergence of Artificial Intelligence (AI) and AR. AI-enhanced AR work instructions combine visual guidance with real-time AI-driven insights. This integration is particularly beneficial in critical processes like quality inspection, where undetected errors could lead to customer safety issues.
Industry adoption trends reveal a strong interest in AR and related technologies. Approximately 30% of industrial manufacturers plan to invest in AR technologies within the next one to three years, while over 40% intend to invest in AI and Machine Learning during the same timeframe.
Microfactories
Manufacturers increasingly embrace decentralised manufacturing models to bolster supply chain resilience as they grapple with inflationary pressures, mounting ESG concerns, and geopolitical uncertainties. This approach involves distributing production across multiple locations, allowing companies to respond more swiftly to local market demands, reduce transportation costs, and enhance overall supply chain robustness.
Microfactories are emerging as a pivotal component of this strategy. These compact, modular manufacturing facilities harness cutting-edge technologies such as artificial intelligence, machine learning, and big data analytics. These technologies enable micro-factories to optimise processes and deliver improved product customisation. The applications for micro-factories are expanding, with various industries recognizing their potential.
For example, London-based Arrival has recently shared its process of using micro-factories to take a different approach to building electric vehicles. Arrival found that their way of providing electric vehicles at a comparable price to ICE powertrains, they needed to produce them near where they are required. Therefore, when companies need vehicles to be adapted to suit localised used cases, this smaller, more adaptable manufacturing technique allows for that.
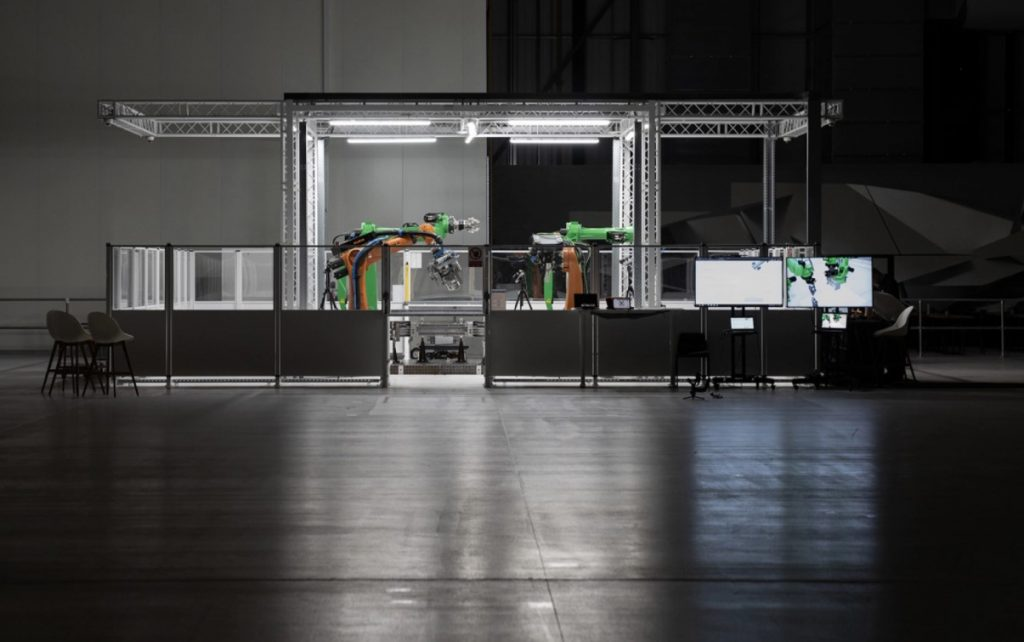
This strategy offers the dual benefits of reducing logistical costs and enhancing supply chain resilience. As we move towards 2025, the adoption of micro-factories is expected to accelerate, reshaping the manufacturing landscape and offering new solutions to longstanding industry challenges.
Cybersecurity Technologies:
The manufacturing industry remains a prime target for cyber threats due to its intricate network of endpoints, outdated systems, and extensive supply chains. The transition from isolated to interconnected systems and the widespread adoption of cloud computing have heightened these vulnerabilities.
For three years running, manufacturing has been the most targeted sector for cyberattacks, accounting for 25.7% of all incidents. Ransomware is involved in 71% of these attacks. With the yearly cost of such attacks rising by 125%, cybersecurity risk now stands as the third most significant external threat for manufacturers.
To address this growing threat, manufacturing organizations are expected to implement several key strategies and technologies in 2025:
Cyber Resilience by Design: Businesses will incorporate cyber resilience into all processes and systems. This risk-based approach will integrate security measures into developing new products, processes, and technologies.
Ecosystem-wide Collaboration: Companies will foster trusted partnerships and increase security awareness among all stakeholders instead of relying on a single organisation to manage security across the supply chain. This collaborative approach will encourage all entities in the business network to work together to tackle cybercrime issues.
Securing IoT Communications: As the Internet of Things (IoT) becomes more prevalent, securing communication protocols will be crucial. Many companies are expected to adopt and strengthen MQTT (Message Queuing Telemetry Transport) with robust encryption, stringent authentication, and tight access controls to ensure data confidentiality between IoT devices.
Multi-layered Defense Strategy: The cyber threats we face in modern times rapidly grow in scale and sophistication. Companies can no longer rely on single-point lines of defence to protect systems but have to employ multiple layers of security measures to remain vigilant and protect their data, applications, networks, and endpoints. Because of this, many manufacturers implement a "defence-in-depth" approach that integrates security measures across all IT systems. This approach closes gaps left by singular security solutions.
The defence-in-depth strategy involves five core pillars that make up the approach.
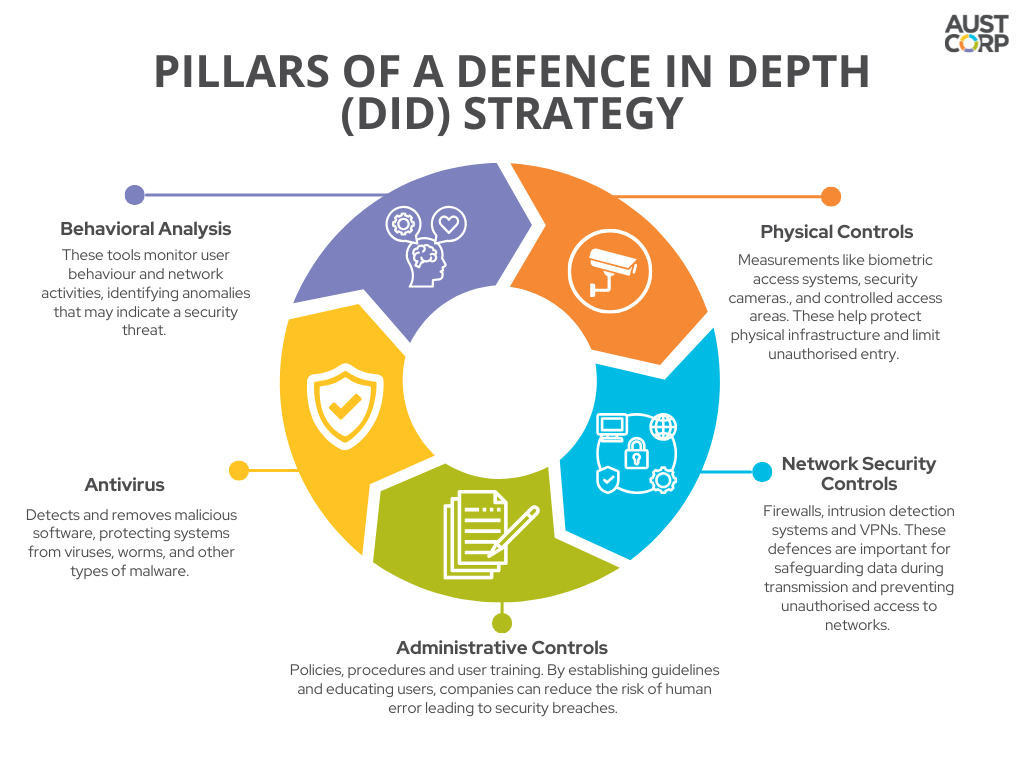
These pillars integrate various defensive measures such as firewalls, intrusion protection systems, SIEM solutions, security gateways, data diodes, endpoint protection, and identity and access management (IAM) systems. By combining these defences, organisations aim to create resilient and adaptable security systems capable of addressing various threats.
Impact of Industry 4.0 Technology Integration on Talent Management in the Manufacturing Sector
The fourth industrial revolution transforms manufacturing by bringing people closer to technology. This revolution creates an environment where physical, digital, and biological fields merge. Advanced technologies like AI, data mining, machine learning, robotics, and blockchain drive change across economies, industries, businesses, and individuals. The widespread use and innovation of these digital technologies are crucial for economic growth and the creation of high-skilled, well-paying jobs in the future.
However, this transformation is not a simple automation process. Employees face cognitive challenges due to changing job roles, motivational challenges adapting to new systems, and emotional challenges as machines take on teaching roles. The rapid pace and broad scope of technological change in Industry 4.0 have pressured employees and businesses to adapt their skill sets quickly.
A noticeable gap has emerged in technical skills, as the education and talent systems are still catching up to integrate the newly required skills in sufficient numbers. Several key trends become apparent when examining the impact of these technological innovations on the manufacturing business landscape.
Re-distribution of work between machines and people:
Work processes are shifting from manual operation to remote observation and management. This change is leading to cleaner, more creative workplaces and the automation of hazardous tasks. Additionally, these technological developments allow employees to interact with intelligent production equipment more efficiently. However, these development opportunities will appear for work to be organised differently, for example, through more flexible and family-friendly working arrangements and more health-friendly workplaces.
Shift in Job Tasks:
As Industry 4.0 rapidly integrates into manufacturing spaces, we're moving towards a greater variety of tasks. Monotonous and physically demanding work is decreasing, while data and information processing tasks are becoming more prevalent. This shift marks a transition from material to information flow. The evolving nature of Industry 4.0 and the tasks that will prevail require new knowledge, skills and responsibilities in key areas of the business:
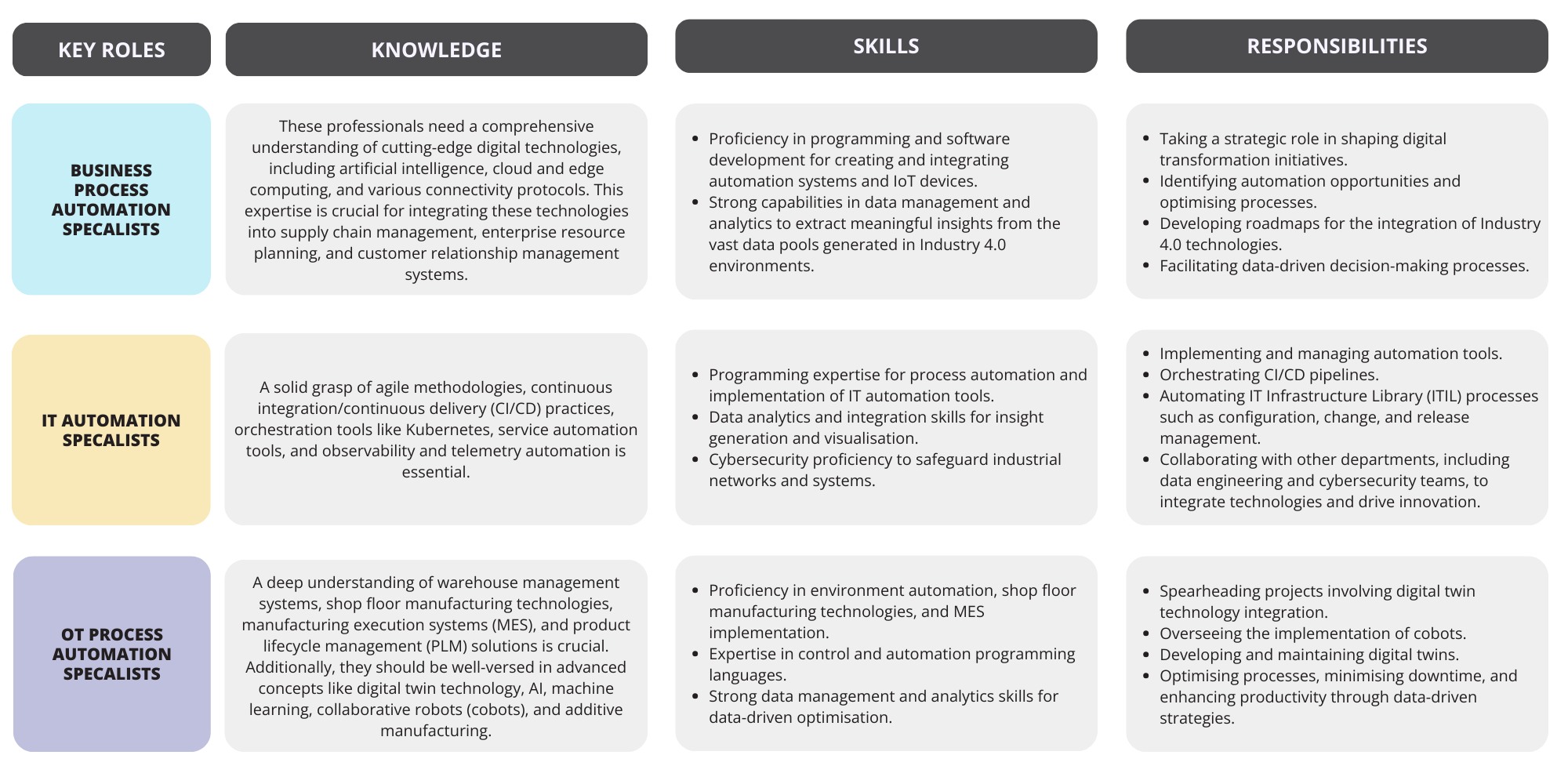
Increased Demand For Soft Skills:
As roles become more complex, involving multiple tasks and effective technology control, soft skills are crucial in Industry 4.0. Studieshave shown that working effectively in this new environment requires broader competencies beyond technical know-how. Modern engineering projects' complexity and client demands call for skills such as commerciality, client management, communication, collaboration, systems thinking, and a stronger external market focus.
Closer collaboration between IT and Operational Departments:
Operational Technology (OT) and Information Technology (IT) systems in a factory have always been separate entities. However, with the increasing trend of Industry 4.0, the line between OT and IT has been blurred, leading to the convergence of both systems. As a result, it is becoming common for OT vulnerabilities that affect IT systems or IT vulnerabilities that affect OT systems. Therefore there is a need for software engineers to understand how their solutions are applied in production, while operators must grasp how they affect their production lines. Interactions between developers and operators should be structured to handle complex IT tasks seamlessly.
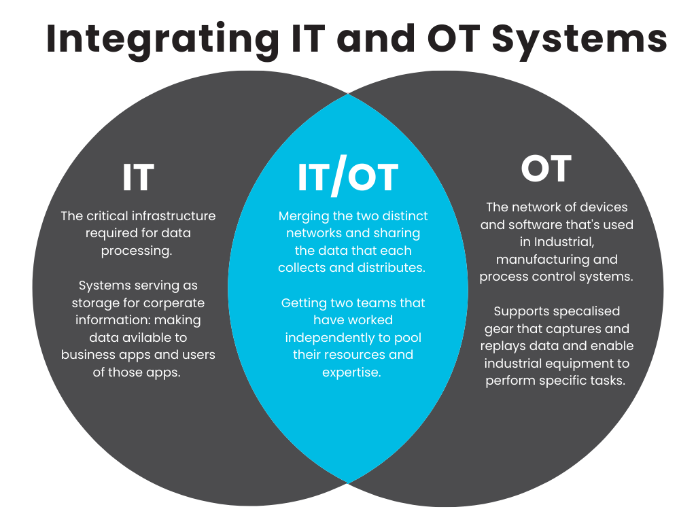
Increased Need For Middle Managers in the Industry 4.0 Era:
While it might be assumed that technical positions are the most critical, middle management functions have emerged as pivotal. Middle managers are crucial in effective change management, making vital connections between strategic planning and implementation. They are key to driving organisational change, employee engagement, and development. As such, managers must develop as talent managers, learning about the benefits of talent management, development, and succession planning.
Increased Need for Active Organisational Identity Management:
In the Industry 4.0 environment, organisations must look ahead to forecast future skill needs. Employer branding supports this by creating a forward-looking image to attract employees with the right skills and qualifications. However, the risk is that a forward-looking employer brand (reflecting what the organisation aspires to become rather than what it was known for in the past) creates a gap between internal and external organisational identities as it can disengage existing employees who are unlikely to identify with this image. Therefore, there is a need for HR managers to implement active organisational identity management for both existing and future employer brands, ensuring that these brands are shared amongst their appropriate audience.
Shift Away From Talent Poaching Towards The "Shared Value" Concept:
This approach aims to build partnerships that extend the talent pipeline into communities while addressing broader training, education, and employment gaps. Some experts have proposed a Talent Supply Chain Management (TSCM) model, which applies supply chain management concepts to talent development and flow within organisations. This approach allows companies to make informed "make and buy" talent decisions, determining what can be developed in-house and what must be acquired externally. Given the difficulty of making accurate predictions in a rapidly changing environment, internal development and external hiring are likely the most effective strategies.
Conclusion
As we've explored, Industry 4.0 is not just a buzzword but a transformative force reshaping the manufacturing landscape. From cloud computing and the Industrial Internet of Things to smart factories and digital twins, these technologies are revolutionising how we produce, manage, and innovate.
However, by 2025, up to 85 million jobs may be displaced by the shift in labour between humans and machines, while 97 million new roles may emerge. This massive transformation is reshaping the very nature of work in manufacturing, from the redistribution of tasks between humans and machines to the increasing demand for soft skills and closer collaboration between IT and operational departments.
The consequences of failing to adapt to these changes are severe. Companies that don't understand and plan for the impact of Industry 4.0 on their talent needs risk falling behind competitors, losing market share, and ultimately becoming obsolete. Your workforce, the backbone of your operations, could find their roles and required skills changing dramatically, almost overnight. The pressure to adapt is immense, and the clock is ticking.
But there's hope. AustCorp Executive is here to help you navigate this complex landscape. With our deep understanding of Industry 4.0 and its impact on talent management, we can help you future-proof your workforce. Our expertise in industrial and manufacturing recruitment allows us to guide you through the changing talent landscape, helping you identify and secure the skills you need to thrive in this new era.
Don't let the Industry 4.0 revolution leave you behind. Contact AustCorp Executive today for a confidential conversation about how we can help you prepare for the future of manufacturing. Together, we can turn the challenges of Industry 4.0 into opportunities for growth and success. Your future-ready workforce is just a call away.
Read More Hiring Tips and Guides
Hungry for more Hiring advice? Check out these relevant blogs to enhance your talent management
Talent Mapping: The Ultimate Guide to Strategic Workforce Planning
The ROI of Employer Branding: How to Create a Compelling Employer Brand
Top 10 Workforce Trends to Watch in 2025: Shaping the Future of Work