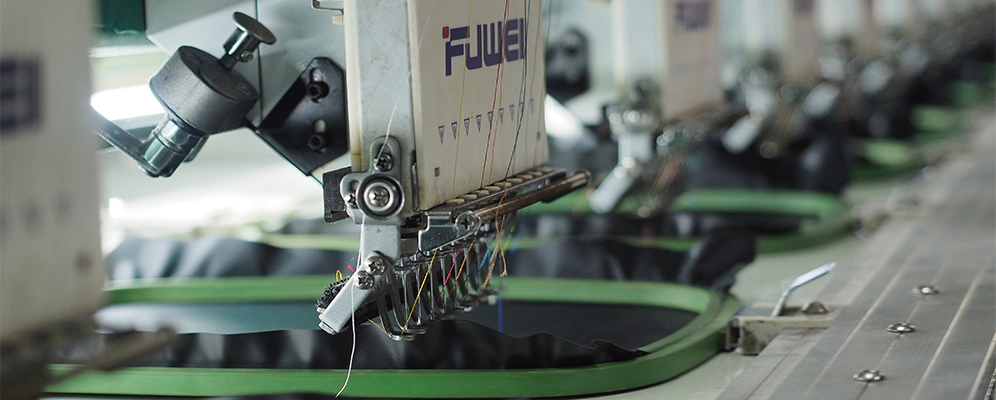
The Rise of Decentralised Manufacturing: Reshaping the Manufacturing Workforce
In 2024, a $139B food manufacturer watched helplessly as a flood paralysed their sole mega-plant—a single point of failure that cost them $28M in downtime and 12% market share. Today, that same company thrives with 89% operational uptime, even amid climate chaos. Their secret? Decentralised manufacturing—a model growing numbers of food manufacturers are racing to adopt.
Supply chain fragility, talent shortages, and consumer demands are converging catastrophically. Transporting finished goods now accounts for a significant portion of operational costs, with logistics expenses rising due to fuel prices and carbon taxes. Meanwhile, 70% of shoppers now prioritise brands that align with local values, abandoning those that ignore regional preference.
Decentralised manufacturing isn't just a gamble—it's a lifeline for manufacturers willing to adapt. By shifting production from centralised facilities to a network of smaller, geographically dispersed units, companies like CSL Limited and Arnott's have demonstrated how blending centralised expertise with localised agility can slash logistics costs through proximity to markets, reduce emissions by shortening supply chains and adopting circular practices and create stable jobs in underserved regions, fostering economic growth.
But this transformation requires more than new facilities—it demands a recruitment and workforce management revolution.
In this blog, we explore the benefits, limitations, and future of decentralised manufacturing and the workforce strategies needed to thrive in this new era.
Ready to explore? Let's dive in.
What is Decentralised Manufacturing?
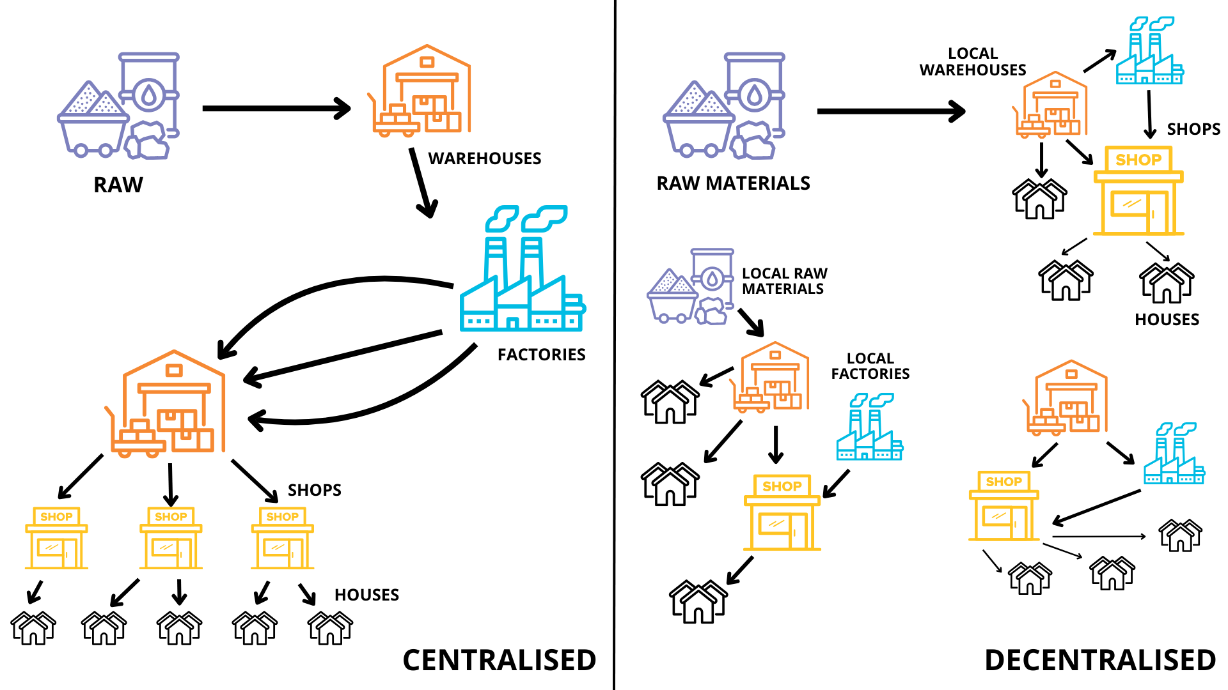
In an era defined by supply chain fragility and hyper-local consumer demands, decentralised manufacturing has emerged as a strategic pivot for manufacturers aiming to future-proof operations. This model shifts production from monolithic, centralised facilities to a network of smaller, geographically dispersed units—closer to raw material sources, labour pools, and end consumer markets.
Unlike traditional setups where a single mega plant serves entire continents, decentralised systems distribute production across regional hubs. These facilities often leverage partnerships with local suppliers, co-manufacturers, and 3PL providers to create collaborative ecosystems.
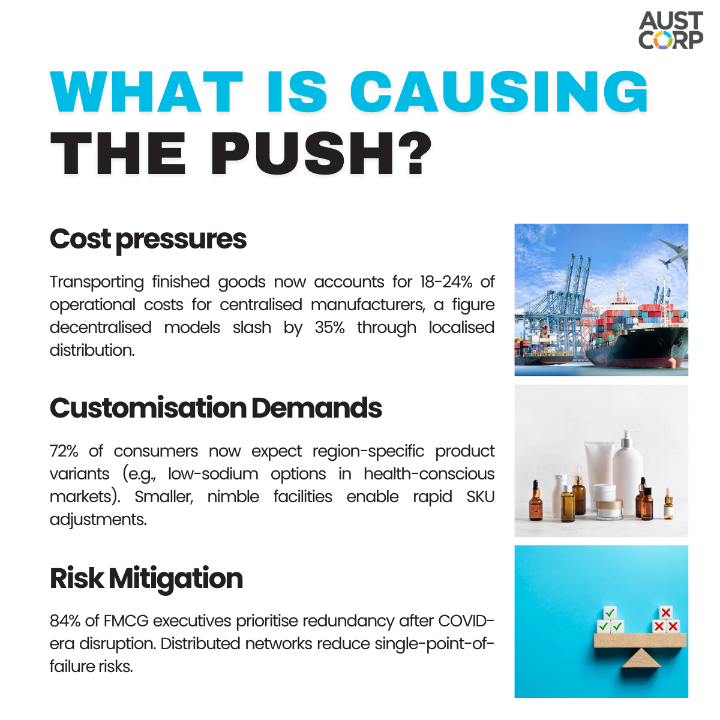
Technical Backbone:
Decentralisation relies on interoperable Industry 4.0 systems—IoT-enabled equipment, blockchain traceability platforms, and cloud-based MES software allow real-time coordination between sites. This creates “Connected autonomy”, where facilities operate independently but share unified data streams for quality control and demand forecasting.
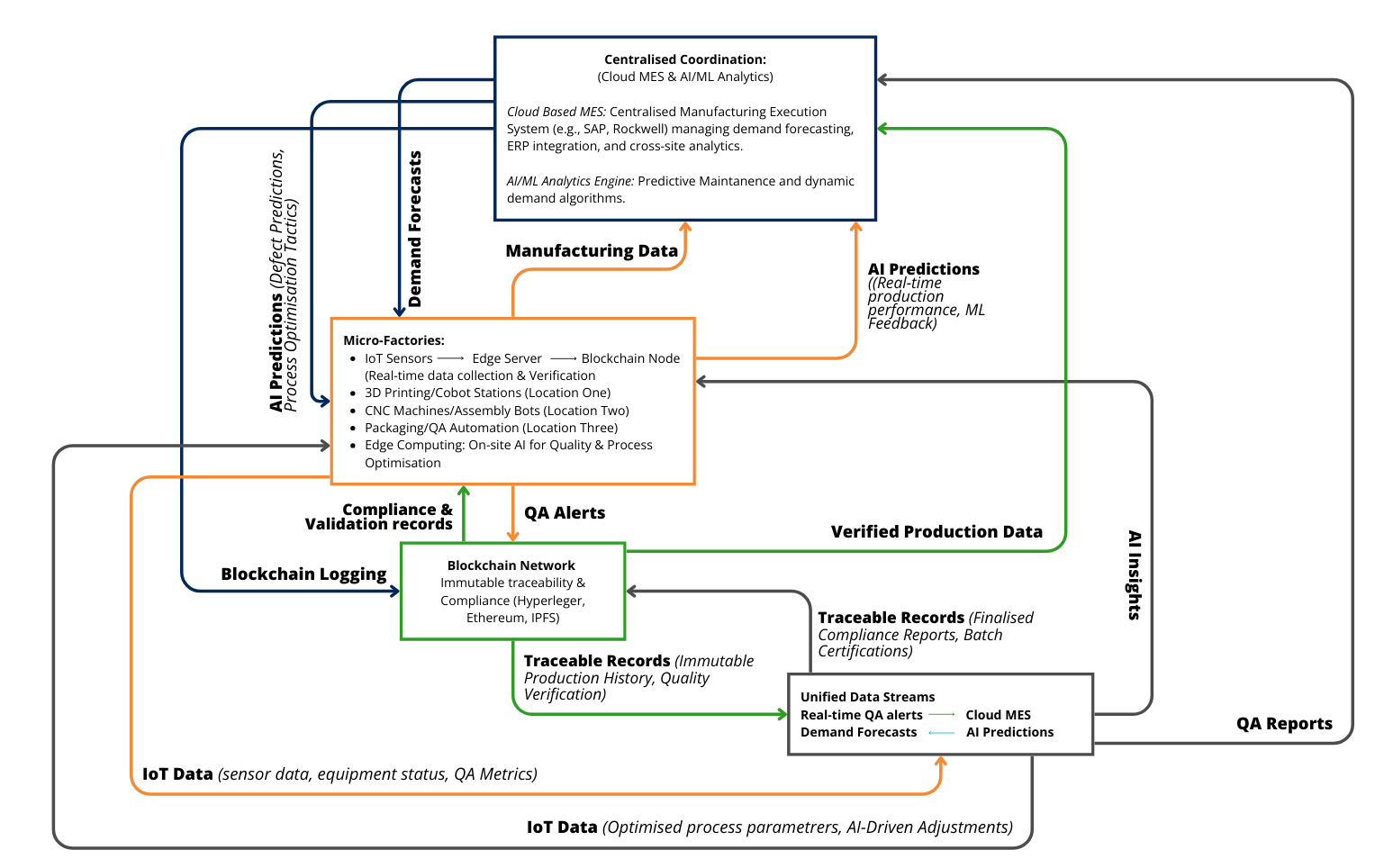
Benefits & Limitations of Decentralised Manufacturing:
Decentralised manufacturing is reshaping how food manufacturers compete and operate, but its adoption requires careful evaluation of trade-offs. Below, we break down the advantages and challenges through the lens of current industry dynamics and talent implications.
Key Benefits:
Market Agility and Customisation:
Localised demand matching: Decentralised manufacturing allows companies to respond more quickly to regional demand by producing market-specific variants closer to end customers. According to Katana MRP, this flexibility enables buisnesses to pivot production based on local preferences, such as low-sodium snacks in health-conscious markets.
Lead Time Reduction: Decentralised hubs positioned closer to customers significantly reduce delivery windows compared to centralised facilities. Sources like Shay Chalmers highlight how these models improve responsiveness by minimising transportation distances and enabling fast fulfilment.
Cost Efficiency:
Logistics Savings: Decentralised manufacturing minimises transportation distances by positioning production facilities closer to end customers. This reduces shipping costs significantly. According to a studyon decentralised warehousing, businesses can reduce overall transportation costs by 15-30% due to shorter delivery routes and proximity to customers.
Inventory Optimisation: By synchronising production with hyper-local demand signals, decentralised systems reduce the need for excess inventory. A study found that decentralised inventory strategies can lower warehousing costs by 15-22%, as businesses avoid overstocking and benefit from real-time demand forecasting.
Risk Mitigation:
Supply Chain Resilience: Distributed networks reduce reliance on single points of failure, making supply chains more robust against disruptions like extreme weather or geopolitical instability. Research highlights that regionalised supply chains enable faster recovery, with companies maintaining uninterrupted operations during disruptions through diversified resources.
Tariff Avoidance: Manufacturing closer to end markets helps companies bypass import duties, which can range from 6-11% depending on the product and destination country. This approach also aligns with trade policies that favour local production.
Sustainability Gains:
Emissions Reduction: Decentralised manufacturing contributes to lower Scope 3 emissions by reducing transportation distances and adopting circular sourcing practices. According to the World Economic Forum, tackling Scope 3 emissions is essential for achieving net-zero goals, with companies reporting significant reductions through localised productions.
Community Impact: Regional hubs create stable jobs in underserved areas, fostering economic growth and stregthening social licences to operate. For example, manufacturers like Dixon Valve have demonstrated how localised facilities generate 45-60 jobs per hub, contributing significantly to local economies.
Key Limitations:
Quality Control Complexities: Ensuring consistent product quality across decentralised facilities remains a significant challenge due to variations in localised processes, equipment calibration, and workforce training. Studies highlight that fragmented ERP systems in distribution networks often create data silos, complicating real-time quality assurance and leading to discrepancies in output. To mitigate this, manufacturers are adopting AI-driven quality tools and blockchain traceability platforms, which harmonise standards by providing centralised oversight through digital twins.
Capital Intensity: Established decentralised networks demand substantial upfront investment in equipment, training, and infrastructure, particularly for industries requiring specalised compliance (e.g., pharmaceuticals). Smaller operators often struggle with ROI timelines due to duplicated resources and site-specific setups, as noted in analyses of decentralised manufacturing costs. To reduce financial barriers, companies are exploring modular micro-factories and shared infrastructure partnerships, such as co-manufacturing hubs, which distribute costs while maintaining regional agility.
Administrative Burden: Managing multi-site operations increases administrative costs by 15-20% compared to centralised models, driven by duplicated HR/QA processes and varying regional regulations. This complexity is amplified in sectors like food and pharmaceuticals, where compliance requirements differ across jurisdictions. Implementing interoperable IoT platforms, such as cloud-based MES software, streamlines coordination by automating real-time data sharing and reducing manual oversight.
Talent Fragmentation: Regional hubs face persistent challenges in attracting specalised skills like automation engineers and sustainability officers, especially in rural areas. A 2024 workforce study revealed that inconsistent training methodologies across decentralised sites exacerbate talent shortages, focusing facilities to rely heavily on upskilling programs. To bridge this gap, forward-thinking manufacturers are building "hub-and-spoke" talent pipelines, rotating specialists between sites, and partnering with regional TAFEs to offer industry 4.0 certifications tailored to local needs.
Sector Specific Implementation Drivers:
Decentralised Manufacturing (DM) adoption varies significantly across industries, shaped by unique operational demands, regulatory landscape, and consumer experiences. Below, we explore how key sectors leverage hybrid models - combining decentralised agility with centralised scale - to address their specific challenges.
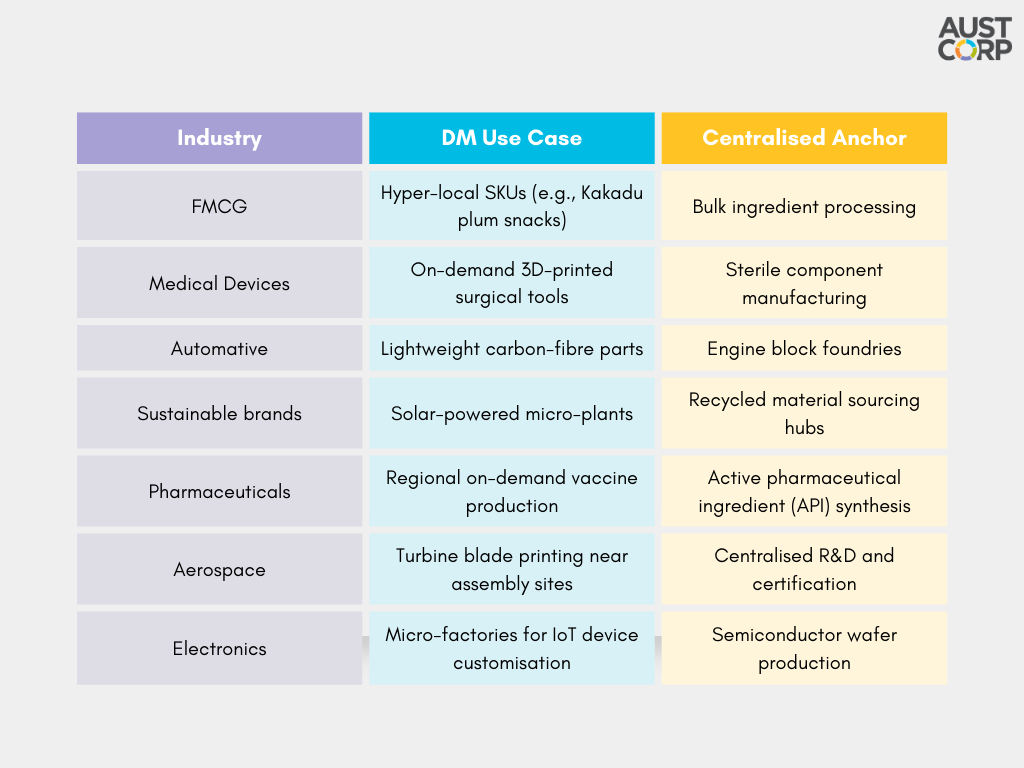
Future Outlook: Decentralised Manufacturing’s Hybrid Evolution
As decentralised manufacturing (DM) matures, its adoption will not replace traditional systems but instead integrate them, creating hybrid architectures that balance scale with agility. Here’s how industries will leverage DM in the 2025-2035 era and the barriers they must overcome.
Hybrid Models:
As the manufacturing sector evolves, hybrid manufacturing models are emerging as a practical solution to balance centralised bulk processing with decentralised customisation. These models allow manufacturers to capitalise on economies of scale while meeting hyper-local consumer demands.
Centralised Core: Centralised facilities continue to handle raw material refinement and large-scale production processes (e.g., flour milling and syrup production). This ensures cost efficiency and consistency for high-volume operations.
Decentralised Edge: Regional hubs focus on final assembly and customisation for market-specific SKUs, such as low-sodium snacks or products featuring Indigenous ingredients. This approach enables manufacturers to respond rapidly to localised consumer preferences while reducing transportation costs and emissions.
Why Hybrid:
Cost Efficiency: Centralised bulk processing leverages economies of scale, reducing per-unit costs by 3% compared to decentralised models. Whereas, decentralised models further slash logistics expenses by positioning production closer to end markets.
Regulatory Compliance: Localised hubs ensure adherence to regional mandates like Australia's TGA standards for Medical Devices, streamlining approvals and quality control.
Sustainability: Hybrid frameworks reduce emissions by minimising transportation distances and integrating circular sourcing, as highlighted in studies on decentralised supply chains.
Workforce & Hiring Challenges Associated with Decentralised Manufacturing
Decentralised Manufacturing presents unique challenges for workforce recruitment and management, requiring innovative solutions to address hybrid recruitment model needs, regional talent disparities, skill gaps, and fluctuating labour demands. This section explores these workforce and hiring challenges in detail, highlighting the complexities of maintaining operational efficiency across distributed sites while adapting to evolving industry needs.
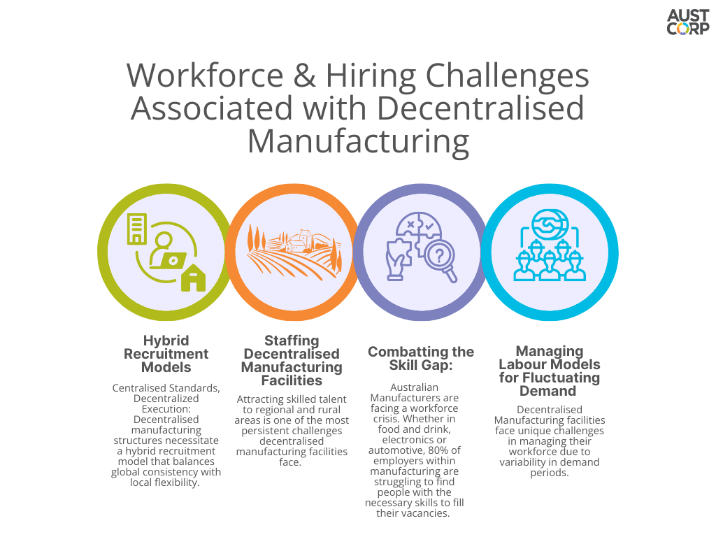
Hybrid Recruitment Models: Centralised Standards, Decentralised Execution:
Decentralised manufacturing structures necessitate a hybrid recruitment model that balances global consistency with local flexibility. This approach is crucial for maintaining brand integrity while addressing the unique needs of distributed production sites. The model incorporates centralised standards for core competencies and employer branding while allowing for decentralised execution to meet local market demands and talent pools.
Why Decentralised manufacturing calls for a hybrid recruitment approach:
Diverse Skill Requirements: DM often involves specalised roles tailored to local production needs, requiring a nuanced understanding of regional talent markets.
Cultural Adaption: Local hiring teams are better equipped to assess cultural fit within specific communities where sites are located.
Agility in Talent Acquisition: Decentralised execution allows faster response to local labour market changes and production demands.
Compliance with local regulations: Local teams are more adept at navigating region-specific labour laws and industry standards.
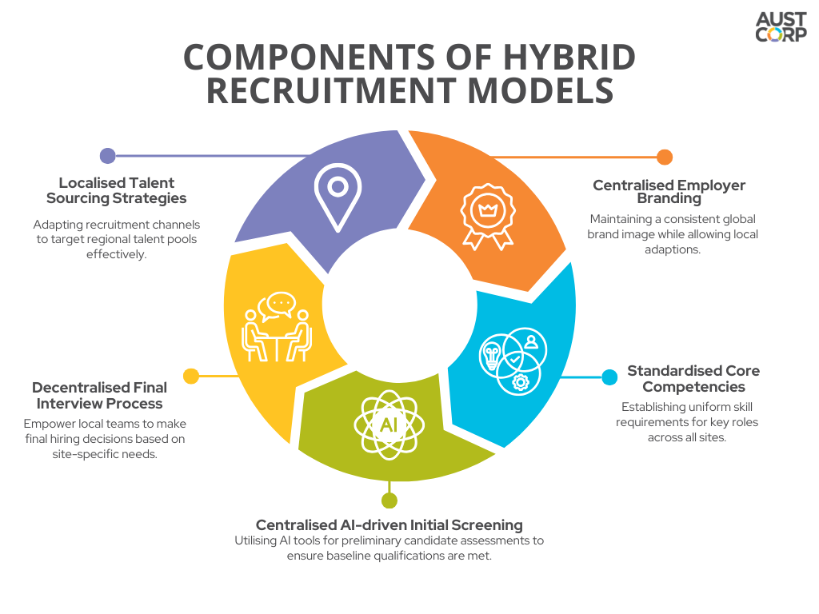
Examples of Australian Manufacturing companies implementing Hybrid Recruitment Models:
BlueScope Steel: BlueScope Steel has adopted a hybrid recruitment model for its decentralised manufacturing operations across Australia. The company centralises its employer branding and core competency assessments, allowing regional sites to tailor hiring processes. This approach has led to a 30% increase in local talent retention in rural areas.
CSL Limited: CSL, a global biotechnology leader, implements a hybrid recruitment strategy for its decentralised plasma collection and manufacturing sites. By centralising their employer value proposition while allowing local customisation, CSL has achieved a 35% reduction in time-to-hire for critical manufacturing roles across their Australian operations.
Arnotts Biscuits: Arnott's has implemented a hybrid recruitment model for its decentralised bakeries across Australia. The company uses centralised AI screening for technical skills assessment while empowering local plant managers to conduct final interviews. This approach has led to a 28% improvement in new hire performance and reduced turnover in regional manufacturing sites.
The Challenge of Staffing Decentralised Manufacturing Facilities
Attracting skilled talent to regional and rural areas is one of the most persistent challenges decentralised manufacturing facilities face. Compared to urban centres, regional locations often experience significant difficulties filling technical and leadership roles, which are critical for maintaining operational efficiency and innovation. These challenges stem from a combination of Labor shortages, infrastructure gaps, and rural locations' inherent disadvantages.
Limited Talent Pools: Regional areas typically have smaller populations and less diverse labour markets, leading to fewer applicants per vacancy. This issue is compounded by the fact that many rural manufacturers rely on local hiring within a limited radius. A report by the Regional Australia Institute highlights that remote regions often lack the industrial diversity and connectivity needed to attract a broader talent base, making it challenging to meet labour demand.
Skill Shortages in Leadership and Technical Roles: According to the Manufacturing Institute, rural manufacturers report that sourcing skilled technical and leadership positions is significantly more challenging than unskilled ones. Many companies struggle to attract candidates with automation, IoT systems, or sustainability management expertise. This shortage forces businesses to expand their search nationally or internationally for these critical roles while relying on local hires for entry-level positions.
Infrastructure Barriers: Rural areas often lack essential infrastructure such as childcare, eldercare, transportation, and affordable housing—key factors influencing relocation decisions. A study by the OECD found that insufficient housing supply dampens enthusiasm among recruits considering moving to rural communities. Additionally, the lack of accessible transportation further limits the mobility of potential workers.
Compensation Challenges: While urban areas face workforce challenges related to high living costs and insufficient compensation, rural employers must offer competitive salaries without exceeding budget constraints. However, even with attractive compensation packages, many candidates remain hesitant due to lifestyle concerns or a lack of professional development opportunities in remote areas.
Labour Force Challenges in Rural Locations: A study conducted by the Manufacturing Institute revealed that 65% of rural manufacturers cite difficulty attracting new employees as their top labour force challenge. Additionally, 53% identified a lack of childcare or eldercare options as a significant barrier. These findings underscore how interconnected systems—such as housing, transportation, and care services—play a crucial role in workforce attraction and retention.
Strategies for Rural Talent Attraction:
To overcome the unique challenges of attracting talent to rural manufacturing hubs, companies can adopt innovative and community-centric strategies:
Localised Employer Branding:
Craft tailored value propositions that align with the rural advantages of the location, such as the cost of living, work-life balance, low criminal rates, and community cohesion. Conduct employee surveys beforehand to identify key workforce issues (e.g., childcare, transportation); you can partner with local organisations to address them or reevaluate your benefits offering to align with workforce needs.
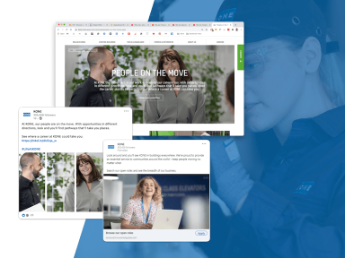
KONE Australia launched a regional EVP campaign in 2020 highlighting work-life balance in rural NSW/VIC hubs. The campaign used geotargeted LinkedIn ads featuring Indigenous partnerships and childcare support. The new EVP was launched through sponsored and organic social media campaigns and updated content across KONE's candidate touchpoints. This campaign increased rural job applications by 50% and boosted a 30% increase in Glassdoor reviews from regional employees.
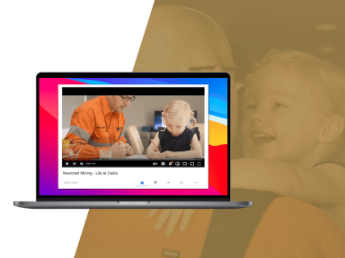
Newcrest Mining is one of the world's leading gold miners, with sites in regional and remote communities worldwide. One of their most extensive operations is in Orange, NSW. To combat an issue of attracting candidates to move to these regional locations, they launched a series of videos that highlighted this attractive lifestyle, both profiling the region itself and telling the real stories of Newcrest employees who have taken advantage of the additional time for family and activities by living closer to the site.
Career Advancement:
Setting clear career pathways can significantly impact your ability to attract talent, specifically in rural areas. For example:
Raise wages to be competitive and develop salary bands and job categories. Demonstrating how much opportunity your company offers can assist significantly when talking with applicants.
Stressing the opportunities to learn and advance in the company should be a key component in your interview process. Highlight cutting-edge technology and the fact that anyone can learn and advance if willing.
This may be coupled with tuition reimbursements and training opportunities, showing your employees where they can go next in their careers and helping them see your commitment to their success.
Flexible Work Models:
Offer shift flexibility (e.g., four-day workweeks, opposing shifts for parents, shorter shifts and more working days) and hybrid roles to accommodate caregiving needs.
BHP introduced its Bamboo Flexible Work program in its Newman, WA facility. The program involved introducing a 7-hour shift (reduced from 12.5 hours) with company housing for employees. The program targeted women and caregivers, offering flexibility for school pickups and drop-offs. The program increased female workforce participation rates from 26.5% (2021) to 34.7% (2024). Additionally, in the Bamboo team, female participation reached 85%, with 25% Indigenous employees.
GLT (Graham Lusty Trailers)introduced a four-day workweek with optional Friday overtime. Additionally, they adjusted shift times to accommodate school hours for parent employees. This initiative improved the attraction and retention of skilled staff in rural QLD and enhanced employee satisfaction.
DEI-Driven Talent Pipelines:
Incorporating DEI strategies into recruitment strategies can widen talent pipelines to meet labour needs. By utilising these strategies, manufacturers can attract people from diverse backgrounds who may not have otherwise considered a career in manufacturing.
Sites located in rural areas often face challenges in meeting their DEI goals related to the workforce because of the limited number of racially diverse candidates in the regions. However, DEI strategies can encompass many dimensions besides race and ethnicity. Rural companies can focus on widening their talent pipelines to include more women, veterans, refugees, second chance and neurodiverse individuals, creating employee resource groups to foster greater community and drive change that leads to more supportive work environments.
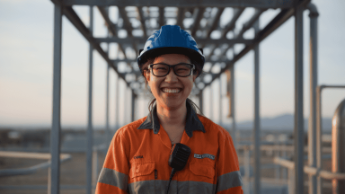
SNF Australia implemented a DEI-based talent initiative that promoted women in male-dominated roles through mentorship programs and standardised salary structures. Additionally, they focused on cultural diversity by recruiting from 14 different nationalities and creating employee resource groups. This initiative increases female representation from 24-30% in technical roles whilst achieving a 30% reduction in turnover due to inclusive work practices. Watch their stories of impact video here.
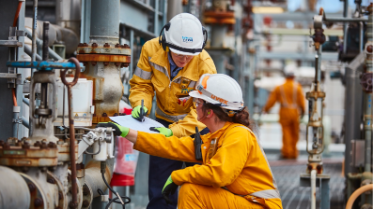
Viva Energy: In 2021/23, Viva Energy was proud to be recognised by the Workplace Gender Equality Agency as an Employer of Choice for the fourth consecutive year, focusing on closing the gender pay gap and providing equal opportunities for their people. They seek equal representation of women and men across the business and have signed up for the 40:40 vision, which is led by the HESTA, which is committed to achieving at least 40% male and 40% female representation within their executive team by 2030.
Some of the initiatives they have implemented to achieve this goal include introducing a superannuation policy designed to bridge the superannuation gap between men and women, providing flexible working options, and designing hiring and workplace processes that are inclusive to all groups including women, indigenous peoples, the LGBT community, culturally diverse candidates, neurodiverse and people with physical disabilities and families.
Bega Group have established a mentoring program for female professionals called the NAWO mentoring program. The program was established by a group of women from logistics, supply chain and manufacturing within Bega to connect women coming through all of those industries. The mentorship program has been successful in facilitating female role models for junior professionals and guidance and advice for women in the industry.
Educational & Community Partnerships:
Another strategy many companies have started implementing is actively involving high schools and community colleges to build talent pipelines. For example,
Working with high schools to increase awareness of job opportunities and support technical paths at community colleges.
Working with local vocational technology programs and even providing students with weekend hours help provide the flexibility needed for them to work while improving their skill sets.
By demonstrating the value of a manufacturing career in terms of stability and opportunity, companies can significantly widen their recruitment pools of tomorrow.
Viva Energy launched school-based apprenticeships in regional QLD, offering students weekend shifts and partnering with TAFE for certification. This resulted in 60+ students placed in IoT/automation roles and a 75% retention rate for apprentices post-certification.
GET ANOTHER EXAMPLE
Fibre Industries (Rural Texas) trained 60+ eighth graders through plant tours and weekend internships, with 40% pursuing manufacturing careers.
Any pictures from the examples
Financial and Lifestyle Initiatives:
Offer competitive wages, housing support and relocation bonuses
The West Virginia Ascend Program provides $12,000 relocation grants and free outdoor recreation packages, and it has attracted more than 200 workers since 2021.
A QLD Manufacturer converted unused dormitories into employee housing, reducing turnover by 18%.
Combatting the Skill Gap:
Australian Manufacturers are facing a workforce crisis. Whether in food and drink, electronics or automotive, 80% of employers within manufacturing are struggling to find people with the necessary skills to fill their vacancies. STAT
The shortage is exacerbated by several factors unique to Australia’s workforce and education system:
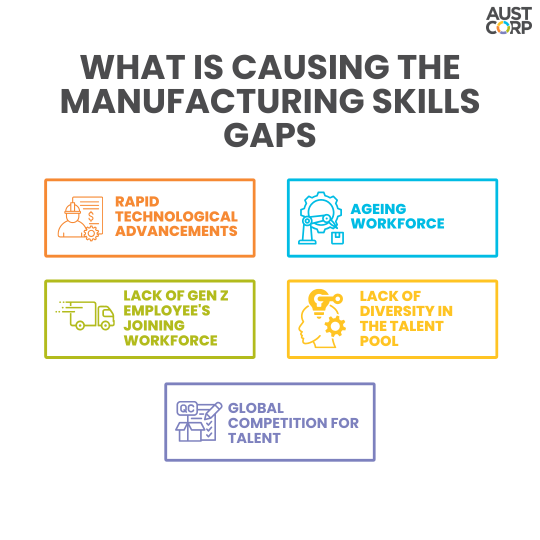
Rapid Technological Advancements: The integration of advanced technologies has fundamentally changed the skills required in manufacturing. Recent estimates show that 87% of manufacturing jobs require digital skills, including automation, data analysis, and programming. However, many workers lack the necessary training to adapt to these changes. For instance, 47% of manufacturers report IoT skill shortages, and only 12% of rural workers meet the technical requirements for IoT and Blockchain roles.
Ageing Workforce: Approximately 40% of the Australian Manufacturing workforce is over 45 years old, with many approaching retirement. This creates a “skill retirement cliff,” where decades of experience and technical knowledge are lost without effective succession planning. Additionally, the average age of manufacturing workers continues to rise, with fewer younger workers entering the industry.
Decline in Apprenticeships and Vocational Training: Apprenticeship completion rates in key trades have fallen significantly, with welding apprenticeship completion rates dropping by 23% annually over recent years. Additionally, the vocational education system has struggled to keep pace with industry needs, with underfunding and outdated curricula leaving many graduates ill-prepared for roles requiring advanced technical skills.
Lack of Diversity in the talent pool: Women, First Nations Australians, and individuals from culturally and linguistically diverse (CALD) backgrounds remain underrepresented in manufacturing roles. Increasing diversity could help address labour shortages but require targeted recruitment and training initiatives. Read more about these strategies later in the article.
Global Competition for Talent: Australia faces stiff competition from other countries for skilled workers. Globally, an estimated 10 million manufacturing roles will remain unfilled due to skill shortages by 2030. Australia’s reliance on skilled migration has been a partial solution but cannot completely close the gap.
Below are some core skills needed within a decentralised manufacturing site/facility. Because sites often use different processes and technologies, skills may vary across sites; however, because the majority of these skills are linked with Industry 4.0 and are, therefore, still new, there are significant skill gaps among all. (ADD SOURCE)
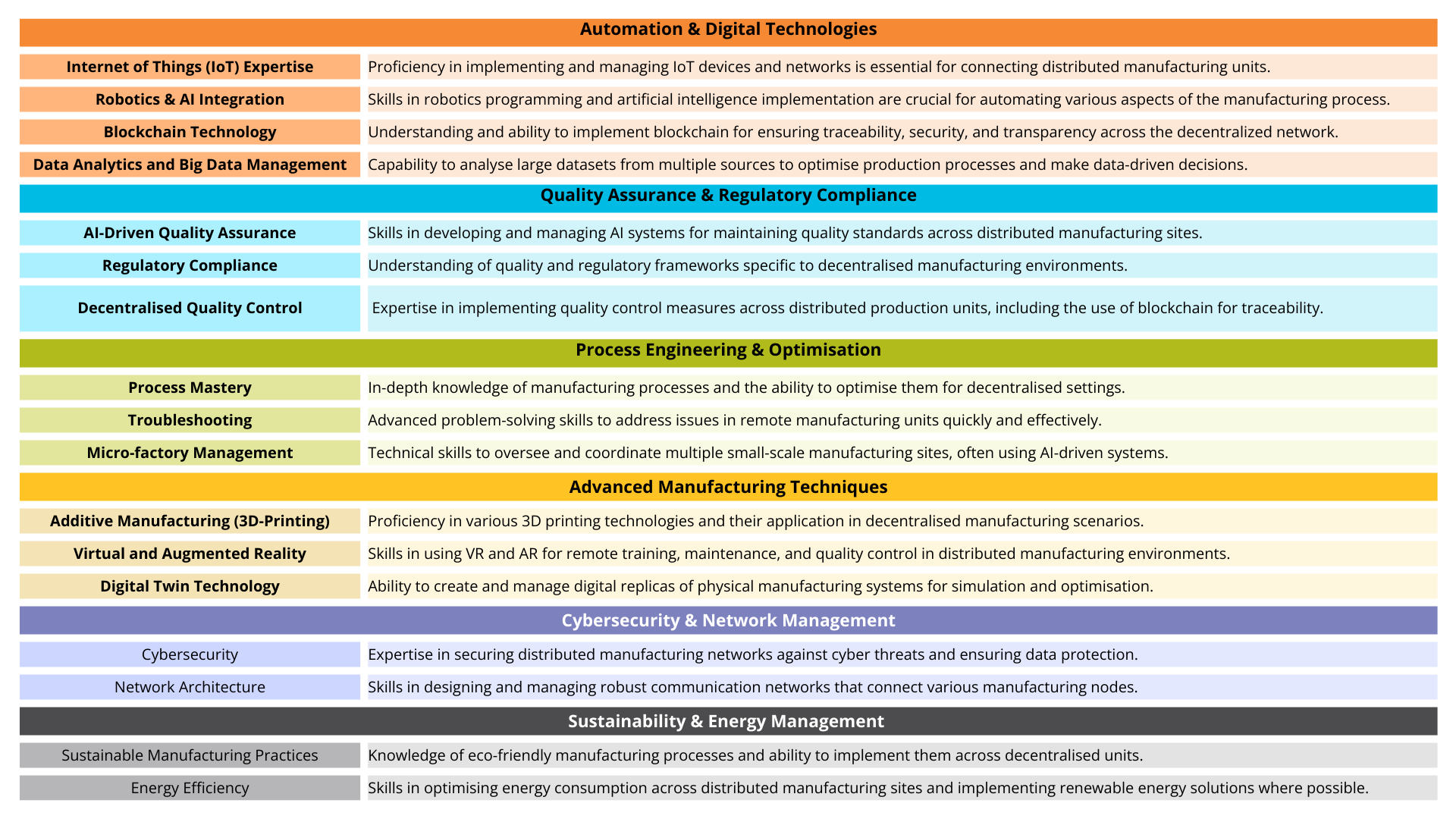
Strategies for combatting these skill gaps:
Skill Development & Partnerships:
One of the most effective strategies for addressing the skills gap in decentralised manufacturing facilities is fostering partnerships between manufacturers, industry bodies, TAFE institutions, and Universities. These collaborations help bridge the gap between skills required by advanced manufacturing technologies and the current workforce capabilities.
Examples of successful partnerships:
Swinburne University and Siemens: Swinburne University partnered with Seimens and the Australian Industry Group to create an Industry 4.0 apprenticeship program. The program integrates vocational trade skills with advanced technologies. Graduates gained hands-on experience working at Seimens and other industry partners, ensuring job readiness. The program has become a benchmark for bridging technical training with higher-level qualifications.
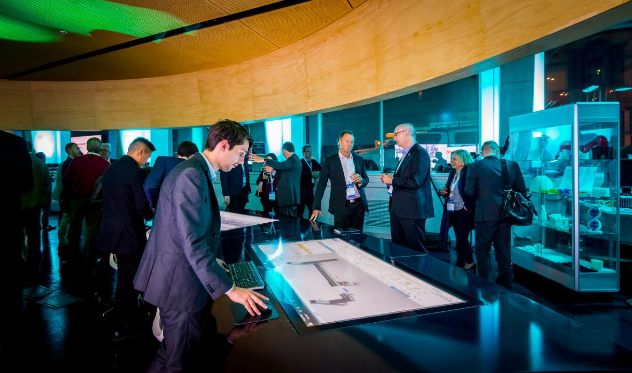
Watkins Steel and BDO Australia: Watkins Steel partnered with BDO Australia to implement a digital transformation strategy that included upskilling its workforce in robotic and automation technologies. The training was conducted in collaboration with local education providers. Watkins Steel created 10 additional jobs for every robotic system commissioned. This investment in workforce development has increased profitability while sustaining employment growth.
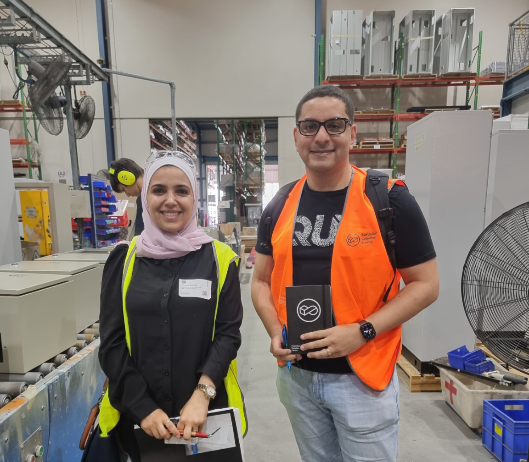
B&R Enclosures: B&R Enclosures partnered with the Australian Cobotics Centre and TAFE Queensland to upskill staff in IoT and automation. Additionally, they launched apprenticeship programs targeting rural youth. This initiative proved successful, with a 40% increase in technical staff certifications and a 22% reduction in defect rates through AI-driven quality control.
In-House Upskilling:
In-house upskilling initiatives are critical for addressing the skills gap in decentralised manufacturing facilities. These programs, designed and facilitated internally by companies, allow manufacturers to tailor training to their specific needs, ensuring their workforce is equipped to handle advanced technologies and processes.
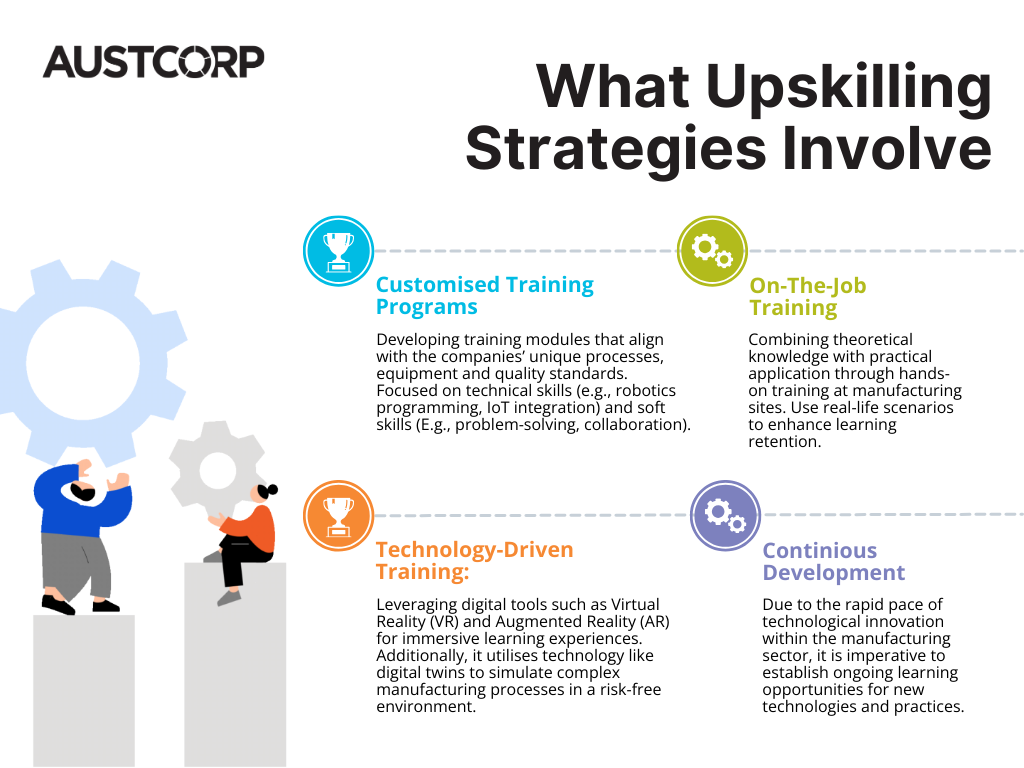
Key Considerations:
Centralised Workforce Training: Decentralised facilities often face challenges maintaining consistent training quality and material across multiple sites. Centralising the development of training materials ensures uniformity while allowing for site-specific adaptions. Strategies like collaborative development of Standard Operating procedures (SOPs), competency-based training frameworks, and cross-jurisdictional standardisation can address these challenges effectively.
Personalisation & Flexibility: Tailoring training programs to individual employees or teams ensures better engagement and skill retention. Additionally, offering flexible schedules for training sessions helps minimise disruption to production workflows.
Examples:
BlueScope Steel:BlueScope Steel developed an internal program to upskill employees in digital technologies like IoT and data analytics. Training sessions were conducted onsite using a combination of e-learning modules using their global learning platform and hands-on workshops tailored to specific roles within their decentralised facilities. The program resulted in a 30% increase in operational efficiency at regional sites and reduced downtime by 25% due to improved troubleshooting capabilities amongst staff.
Bega Cheese: Bega Choose implemented an in-house upskilling program to train employees on automation technologies in its decentralised dairy processing plants. The initiative included partnerships with technology vendors for equipment-specific training and internal workshops facilitated by senior engineers. The program reduced production errors by 20% and improved employee retention by 15%, as workers felt more confident operating advanced machinery.
Visy Industries: Visy Industries developed an internal sustainability training program to improve energy efficiency practices across its decentralised packaging plants. Employees participated in workshops on energy optimisation techniques and waste reduction strategies tailored to their specific roles. The program achieved a 15% reduction in energy consumption across all sites within two years.
Government Initiatives:
Initiative | What is it | Who it Helps | Success/Challenges |
Introduced by the Albanese Government, the Fee-Free TAFE initiative provides free access to vocational education and training (VET) courses in priority areas, including advanced manufacturing and digital technologies. | Priority groups such as women, Indigenous Australians, young people, and those in regional areas. | Success: Over 568,400 Australians enrolled in Fee-Free TAFE courses by early 2025, with 33% of enrolments from regional and rural areas. | |
Tafe NSW established Centres of Excellence for Manufacturing campuses in Western Sydney, Newcastle, and Wollongong. These centres focused on developing critical skills like advanced manufacturing, logistics, defence, and renewable energy through partnerships with industry leaders. | | The initiative has improved access to cutting-edge training technologies and created seamless pathways from TAFE to university education. It is expected to significantly uplift core skills across NSW’s manufacturing workforce starting in 2025. | |
A five-year agreement starting in 2024 allocates $12.6 billion from the federal government to expand access to VET programs. The NSA focuses on high-quality vocational education tailored to industry needs. | Regional manufacturers, apprentices, trainees, and workers require upskilling or reskilling. | Success: The NSA emphasises cooperation between states and territories to address local skill shortages while supporting national-priority industries like manufacturing. Challenges: Previous agreements faced criticism for not sufficiently increasing skill levels or qualifications. The NSA aims to improve outcomes through better coordination and targeted investment. | |
A Queensland Government Initiative providing $16.5 million in funding to support employers, apprentices, and trainees in manufacturing through targeted training and skill development programs. | Regional Manufacturers seeking advanced manufacturing capabilities and workers needing digital skills training. | Success: MSQ has identified key skill gaps in manufacturing and delivered training aligned with industry demand, helping businesses transition to advanced manufacturing technologies. | |
A Victorian Government initiative worth $4.5 million was created in late 2022 that funds partnerships between training providers and industries to deliver tailored training programs for priority sectors like manufacturing. | Manufacturing businesses need workforce upskilling in areas like digital technologies and sustainability practices. | Success: Since starting, the program has offered courses in 13 fields, including AI, data analytics, cyber security, and software development, with specialist courses in robotic process automation, computer-aided design, or manufacturing and additive manufacturing. Challenge: Ensuring the long-term sustainability of these programs as industries evolve rapidly. | |
A Tasmanian Government program supports non-accredited training activities for advanced manufacturing enterprises to develop workforce capabilities. | Tasmanian manufacturers transitioning to advanced manufacturing processes. | Success: The program has helped many businesses adopt new technologies while equipping workers with the necessary skills for sustainable growth. |
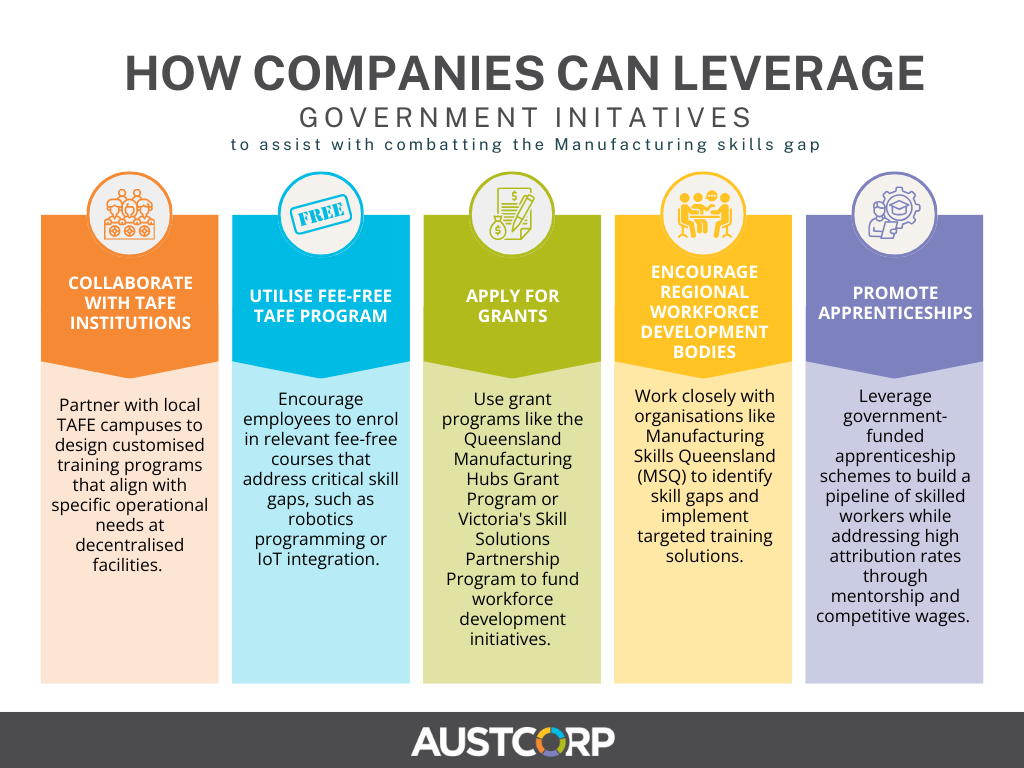
By leveraging these strategies of Skill Development & Partnerships, In-House Upskilling, and Government Initiatives to combat the skill gaps associated with decentralised manufacturing, manufacturers can build a resilient workforce equipped to meet the demands of modern decentralisation operations while contributing to regional economic growth.
Managing Labour Models for Fluctuating Demand in Decentralised Manufacturing Facilities:
Decentralised Manufacturing facilities face unique challenges in managing their workforce due to variability in demand periods.
This is because:
Demand variation across sites: Decentralised facilities often serve diverse markets, leading to differing production schedules and demand surges at various locations. This requires tailored labour solutions for each site.
Geographical Dispersion: Facilities located in regional or rural areas may face additional challenges in attracting and retaining skilled workers, making scalable labour solutions essential.
Specialised Skill Requirements: Advanced technologies like robotics, IoT, and automation require a mix of highly skilled workers for baseline operations and temporary specialists for project-based tasks or peak periods.
Cost Management: Overstaffing during low-demand periods increases operational costs while understaffing during peak times can lead to production delays and missed revenue opportunities.
These fluctuations require dynamic labour models that balance baseline staffing needs with the flexibility to scale up during peak periods. A common approach is to use Full-Time Employees (FTEs) for steady, ongoing operations and supplement them with labour hire services during high-demand periods.
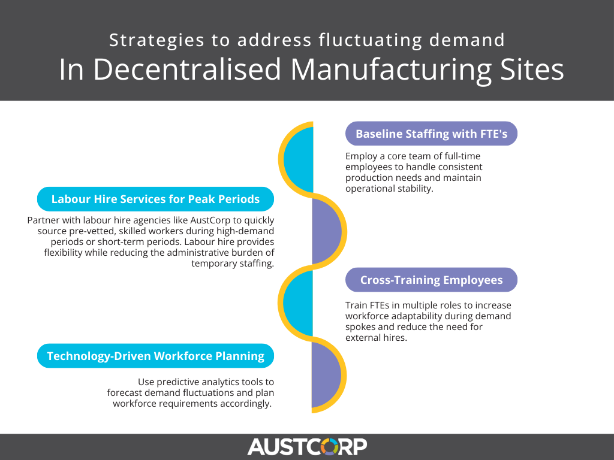
Conclusion
Decentralised manufacturing isn't just a trend—it's an imperative for Australian manufacturers competing in an era of climate volatility, fragmented consumer demands, and supply chain fragility. Companies mentioned in the blog prove that hybrid models blend the best of centralised efficiency and localised agility, delivering lower logistical costs, fewer emissions, and increased product customisation for manufacturers.
Yet success hinges on overcoming workforce challenges, such as skill gaps in advanced technology, regional talent shortages, and fluctuating demand requiring agile labour models.
The solution lies in adaptive talent strategies - TAFE partnerships for Industry 4.0 certifications, DEI-driven pipelines for underrepresented groups, and hybrid recruitment frameworks that balance global standards with local needs.
Manufacturers that invest in decentralised-ready workforces will dominate sectors like sustainable packaging, precision fermentation, and Indigenous Ingredient processing. Those who delay risk becoming cautionary tales.
Will you get ahead or be left behind?
Future-Proof Your Workforce with AustCorp
Australia's $212B manufacturing sector is reinventing itself - don't let talent gaps leave you behind.
Why Partner With Austcorp?
Strategic Headhunting: Tap into our 25-year industrial network to secure niche roles like Automation Architects and Micro-Factory Directors—experts in IoT, blockchain, and crisis management.
Proactive Talent Pipelines: We forecast trends and pre-vett candidates, so you’re ready for tomorrow’s skill demands.
Regional Employer Branding: We utilise geotargeted campaigns attracting talent within 50km of your hubs. Additionally, our marketing team works with various parties, including your company and local community groups, as well as utilising AI sentiment analysis to tailor messaging to regional values whilst ensuring it aligns with the company and role characteristics.
On-Demand Labour: Deploy pre-vetted contractors in 48 hours - we handle payroll, compliance, and quality control.
Hybrid decentralised manufacturing demands hybrid talent strategies. Let us shoulder the complexity while you focus on production.